bodywork welding sheet metal tig On this episode of Make It Kustom I show you how to butt weld thin sheet metal body panels using tig welding. This is a fender repair on a customers Fox body.
An ammo box is, IMHO, an ideal storage container. After all, ammo itself is stored tightley packed in them and that includes both primers and powder! If a light steel ammo box is safe for military ammo, including rockets and grenades, it's safe for primer storage too.
0 · welding tig sheet metal
1 · welding thin metal body parts
2 · welding metal body parts
3 · welding auto body sheet metal
4 · tig welding auto sheet metal
5 · tig welding auto body sheet
6 · tig welding auto body
7 · mig and tig welding
Metal Supermarkets Wichita is your one-stop metal supplier with over 8,000 metal types, shapes, grades and sizes. From aluminum and stainless steel and even rare metals, you can find everything you need in one place. Buy metals online for pick up, call us to have an order delivered, or browse through our warehouse.
One benefit of TIG welding is that the weld bead can be kept very small, ideally no more than 1-1/2 times the material thickness, and the welds are soft enough to work with a .
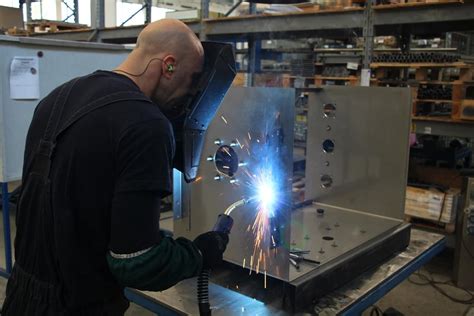
20 x 25 in electrical box
To weld sheet metal with solid wires, use electrode positive (EP, or reverse . After all, so-called TIG welding (for tungsten inert gas) is also a metal-inert-gas welding process. Properly, what is called MIG should be called according to the American . To weld sheet metal with solid wires, use electrode positive (EP, or reverse polarity). Don’t attempt to weld thin materials like sheet metal with flux-cored wires, which put .

welding tig sheet metal
Did you know that TIG welding is the best option for sheet metal? The biggest problem any welder is going to face when it comes to sheet metal is the heat in. On this episode of Make It Kustom I show you how to butt weld thin sheet metal body panels using tig welding. This is a fender repair on a customers Fox body.
Whether working on automotive body panels, HVAC components, or artistic metalwork, the ability to dial in the perfect TIG welding settings sets the stage for impeccable craftsmanship. Factors Affecting TIG Welding Sheet . As a rule, when MIG welding sheet metal, never use a body filler metal that is thicker than the base metal. It is recommended that a welder should use .023- or .024-inch wire for light gauge sheet metal work. . Sheet Metal . Most welders avoid welding thin metal with the stick welding process. It’s difficult to control your heat input and very easy to burn through the material. Stick welding is not a delicate process but with a proper setup and . In general, though, TIG welding sheet metal can be done like TIG welding any other metal. Get your amps going, stick to a consistent travel speed and dab, dab, dab. . Thanks to being unable to totally stop warpage, being .
welding thin metal body parts
welding metal body parts
One benefit of TIG welding is that the weld bead can be kept very small, ideally no more than 1-1/2 times the material thickness, and the welds are soft enough to work with a hammer and dolly. This allows you to smooth out any distortion the welding may have caused.

How to Weld Auto Body Sheet Metal With a TIG Welder. The best two electrodes for welding auto body sheet metal are either ceriated tungsten or thoriated tungsten. Ditch a 1/8-inch tungsten electrode for something much smaller, like 1/16-inch tungsten — it will give you a lot more control over the whole process, and it is more forgiving in .
After all, so-called TIG welding (for tungsten inert gas) is also a metal-inert-gas welding process. Properly, what is called MIG should be called according to the American Welding Society (AWS) GMAW for gas metal arc welding. TIG is properly designated as GTAW, for gas tungsten arc welding. I’m glad to get all of that sorted out, thank you.
To weld sheet metal with solid wires, use electrode positive (EP, or reverse polarity). Don’t attempt to weld thin materials like sheet metal with flux-cored wires, which put more heat into the base metal. TIG welding sheet metal. Forget the larger 1/8-inch tungsten electrode and use a smaller one.Did you know that TIG welding is the best option for sheet metal? The biggest problem any welder is going to face when it comes to sheet metal is the heat in.On this episode of Make It Kustom I show you how to butt weld thin sheet metal body panels using tig welding. This is a fender repair on a customers Fox body. Whether working on automotive body panels, HVAC components, or artistic metalwork, the ability to dial in the perfect TIG welding settings sets the stage for impeccable craftsmanship. Factors Affecting TIG Welding Sheet Metal Settings. . When TIG welding sheet metal, it’s essential to maintain a steady hand and precise control over the .
As a rule, when MIG welding sheet metal, never use a body filler metal that is thicker than the base metal. It is recommended that a welder should use .023- or .024-inch wire for light gauge sheet metal work. . Sheet Metal TIG Welding Tips. 1 for 1 rule: The best way to estimate the heat input needed for welding is by applying the 1 for 1 . Most welders avoid welding thin metal with the stick welding process. It’s difficult to control your heat input and very easy to burn through the material. Stick welding is not a delicate process but with a proper setup and rod size, you can weld sheet metal with the SMAW. Unlike MIG and TIG, stick welding doesn’t require a shielding gas.
In general, though, TIG welding sheet metal can be done like TIG welding any other metal. Get your amps going, stick to a consistent travel speed and dab, dab, dab. . Thanks to being unable to totally stop warpage, being able to go over it with a dolly and body hammer is one way to flatten your metal back out. This is possible with a TIG weld . One benefit of TIG welding is that the weld bead can be kept very small, ideally no more than 1-1/2 times the material thickness, and the welds are soft enough to work with a hammer and dolly. This allows you to smooth out any distortion the welding may have caused.
How to Weld Auto Body Sheet Metal With a TIG Welder. The best two electrodes for welding auto body sheet metal are either ceriated tungsten or thoriated tungsten. Ditch a 1/8-inch tungsten electrode for something much smaller, like 1/16-inch tungsten — it will give you a lot more control over the whole process, and it is more forgiving in . After all, so-called TIG welding (for tungsten inert gas) is also a metal-inert-gas welding process. Properly, what is called MIG should be called according to the American Welding Society (AWS) GMAW for gas metal arc welding. TIG is properly designated as GTAW, for gas tungsten arc welding. I’m glad to get all of that sorted out, thank you. To weld sheet metal with solid wires, use electrode positive (EP, or reverse polarity). Don’t attempt to weld thin materials like sheet metal with flux-cored wires, which put more heat into the base metal. TIG welding sheet metal. Forget the larger 1/8-inch tungsten electrode and use a smaller one.
Did you know that TIG welding is the best option for sheet metal? The biggest problem any welder is going to face when it comes to sheet metal is the heat in.
welding auto body sheet metal
On this episode of Make It Kustom I show you how to butt weld thin sheet metal body panels using tig welding. This is a fender repair on a customers Fox body. Whether working on automotive body panels, HVAC components, or artistic metalwork, the ability to dial in the perfect TIG welding settings sets the stage for impeccable craftsmanship. Factors Affecting TIG Welding Sheet Metal Settings. . When TIG welding sheet metal, it’s essential to maintain a steady hand and precise control over the . As a rule, when MIG welding sheet metal, never use a body filler metal that is thicker than the base metal. It is recommended that a welder should use .023- or .024-inch wire for light gauge sheet metal work. . Sheet Metal TIG Welding Tips. 1 for 1 rule: The best way to estimate the heat input needed for welding is by applying the 1 for 1 . Most welders avoid welding thin metal with the stick welding process. It’s difficult to control your heat input and very easy to burn through the material. Stick welding is not a delicate process but with a proper setup and rod size, you can weld sheet metal with the SMAW. Unlike MIG and TIG, stick welding doesn’t require a shielding gas.
tig welding auto sheet metal
The fourth black hot wire appears to feed toward the fan wall switch (exiting the box at the top right). The switch switches that hot line and sends the switched power back to this box on the white wire (part of the top right bundle).
bodywork welding sheet metal tig|welding tig sheet metal